Bry-Air BVL Series automatic vacuum loaders offer large savings to plastics processors, both in terms of man-hours and material by automating the transfer of plastic pellets from shipping containers and storage bins to the processing machines.
Twin Auto Loaders are CNC manufactured with powder coated finish. They have unique silicon and SS flapper design with heavy duty regenerative vacuum pump.
The three combinations available in twin loader are:
- Flapper & Flapper Type Receiver: When both the primary as well as secondary receivers are mounted on the Hoppers for conveying undried material to two drying hoppers.
- Flapper & JIT (Just in Time) Type Receiver: When one receiver is mounted on the Hopper for loading undried material and the secondary receiver directly on the throat of the machine for conveying dried material.
- JIT (Just in Time) & JIT (Just in Time) Type Receiver: When both the primary as well as secondary receivers are mounted directly on the throat of the machine for conveying dried material.
Bry-Air Twin Loader ensures that the material is always available at both the primary and secondary receivers. These loaders are designed for conveying undried and dried material at both points. When the power is switched ON i.e., when the start key is pressed, the vacuum blower starts and the solenoid valve of the primary receiver gets energised starting the primary loadings. After completion of primary loading, the solenoid valve of the secondary receiver gets energised and secondary loading starts. At the same time, the primary receiver belly dumps material into the hopper and a signal goes to the controller for the next cycle.
After completion of both cycles, primary as well as secondary, the controller checks at which station material is required. If the primary loader doesn’t need more material, the controller will switch over the loading to the secondary loader and vice versa. If both stations do not require material, after a set delay time vacuum blower stops. Whenever the material is required by any station, the blower starts again and works as per the above sequence.
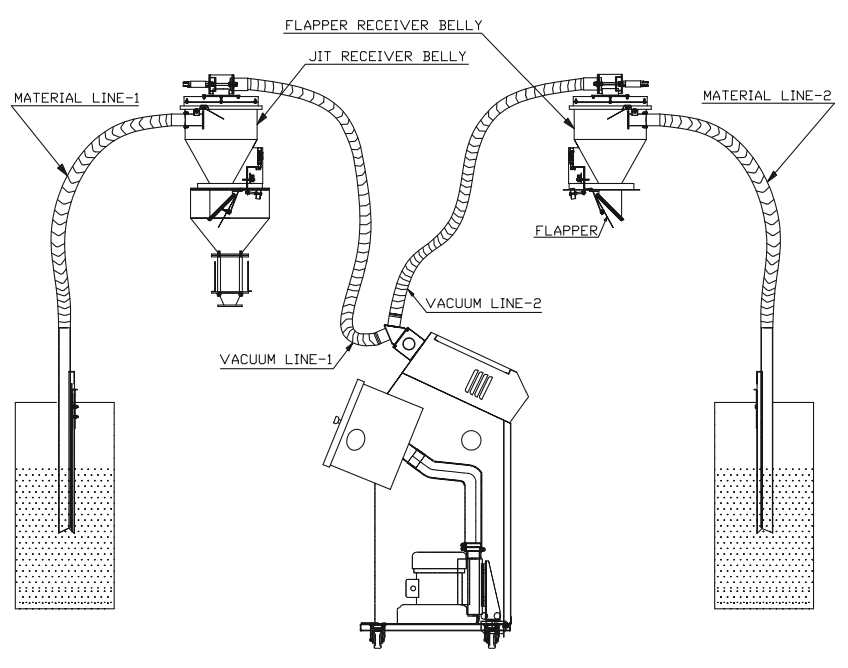
Model
|
Conveying Line Size Dia (mm)
|
Vacuum Line Size Dia (mm)
|
Fiter Type
|
Full Load Amp. at 415/3/50
|
Blower
KW
|
Receiver Belly Dimensions (mm)
|
Trolley Dimensions (mm)
|
Approx. Shipping
Weight
(Kg)
|
Ltr.
|
H
|
D
|
W
|
D
|
H
|
BVL-100 (T)
|
32
|
50
|
Cartridge
|
2.14
|
1.30
|
6
|
410
|
200
|
340
|
460
|
955
|
85
|
BVL-200 (T)
|
38
|
50
|
Cartridge
|
3.9
|
1.75
|
6
|
505
|
314
|
376
|
508
|
1030
|
105
|
BVL-300 (T)
|
38
|
50
|
Cartridge
|
3.9
|
1.75
|
15
|
505
|
314
|
376
|
508
|
1075
|
105
|
BVL-500 (T)
|
50
|
50
|
Cartridge
|
8.2
|
4
|
30
|
645
|
314
|
450
|
620
|
1075
|
130
|
BVL-1000 (T)
|
50
|
63.5
|
Cartridge
|
8.0
|
4*
|
30
|
645
|
314
|
680
|
1130
|
1270
|
165
|
BVL-1500 (T)
|
50
|
63.5
|
Cartridge
|
12.0
|
5.5*
|
30
|
645
|
314
|
680
|
1130
|
1270
|
185
|
BVL-2000 (T)
|
63.5
|
63.5
|
Cartridge
|
15.60
|
7.5
|
30
|
645
|
314
|
680
|
1130
|
1270
|
195
|
“Oil & Moisture Free Compressed Air @ 4 to 6 bar is required”
*Double stage impeller high pressure blower
|
BVL-1000 (F) / 1500 (F) / 2000 (F) — Without caster wheels
|
All data subject to change without notice
Cabinet-style, floor mounted twin auto loaders come with standard:
- Material receiver belly for primary and secondary loading
- Quick removable clamps for material and vacuum hoses
- Micro PLC controller to supervise the operation, faults management along with display messaging of system parameters of twin loader
- Pneumatic actuated cylinder to change the vacuum from primary receiver to secondary
- Service window for easy service of receiver belly in case of JIT Receiver
- CRS receiver and SS as optional
- Flexible, transparent hoses of PVC/ PU material for visibility of conveying material
- Cartridge-type dust replant high-efficiency paper filter
- Adjustable material pick-up tube for air-to-material ratio
- Audible alarm with a message for faults like material shortage & pump tripped
- Password facility to avoid any kind of unauthorised handling
- SS Mesh Filter of 530 microns separates the resin from the air in the receiver belly
- ATM valve helps in avoiding frequent on/off of vacuum pump
- Global leader Siemens makes electrical switchgear for safety and reliability
- Option available for pneumatically operated ratio loading & vacuum takeoff box
- Integrated limit-switch activates material demand
- C-Clamp for easy removal of the top hood in the receiver belly for easy cleaning